فرآیند گالوانیزه گرم چیست؟
ورق های گالوانیزه امروزه کاربردهای بسیاری را در صنعت به خود اختصاص داده اند و این موضوع به علت خواصی است که به سبب فرآیند تولید در ساختار و شکل ظاهری آن ها ایجاد می شود. از جمله رایج ترین این خواص، داشتن مقاومت در برابر عواملی مانند آب، رطوبت، زنگ زدگی و خوردگی می باشد که بسیاری از فولادها از آن بهره مند نمی باشند. برای ایجاد این گونه ویژگی ها در یک محصول تخت فولادی نیاز به انجام فرآیندی به نام گالوانیزاسیون می باشد که دو روش دارد.
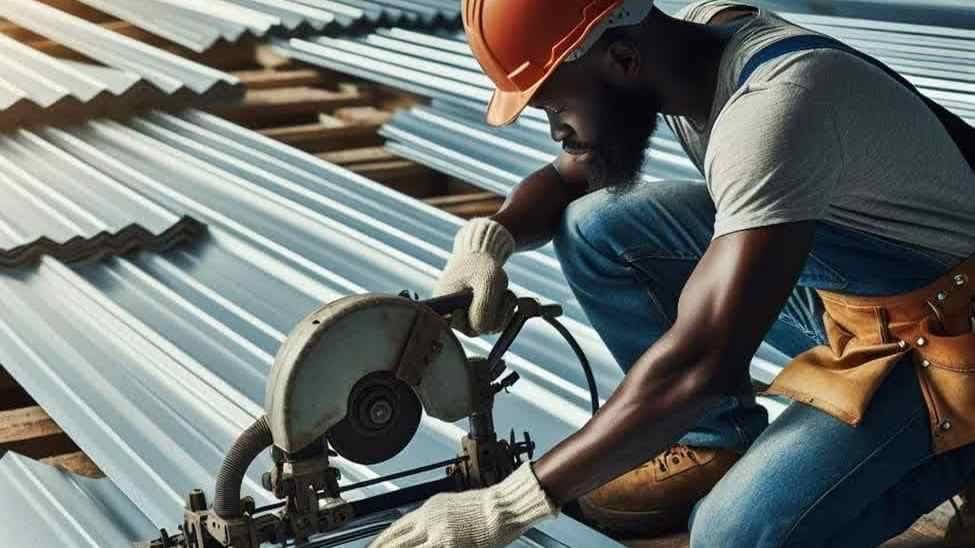
این دو روش با نام های گالوانیزه گرم (Hot galvanizing) و گالوانیزه سرد (Cold galvanizing) شناخته می شوند. با انجام این دو فرآیند یک لایه پوششی برای محافظت از فلز پایه بر سطح فولاد اعمال شده و از آن در برابر این گونه عوامل محافظت می کند. حال برای بررسی چیستی فرآیند گالوانیزه گرم در ادامه به بررسی تفاوت آن با گالوانیزه سرد، مشخصات ، تاریخچه، مراحل و مزیت هایی که با انجام این روش همراه هستند، پرداخته ایم.
با این وجود شرح خلاصه ای از گالوانیزه گرم شامل غوطه ور کردن مواد اولیه در حوضچه هایی با دمای بالا در حدود 450 درجه سانتی گراد است. این حوضچه ها درون خود محلولی از جنس فلز روی دارند؛ زیرا این فلز برای فولاد اولیه که هادی یا کاتد است، به عنوان آند عمل کرده و از سطح در برابر زنگ زدگی و خوردگی حفاظت می کند.
سه مرحله اصلی انجام این فرآیند نیز شامل آماده سازی فولاد ابتدایی، گالوانیزاسیون و عملیات تکمیلی و بازرسی شیت ها می باشد. در واقع با ایجاد واکنش میان فولاد و روی مذاب به شکل متالورژیکی، یک پوشش آلیاژی مستحکم همراه با مقاومت و طول عمر بالا بر روی فلزات ایجاد شده و محصولات نهایی نیز ورق گالوانیزه نامیده می شوند.
تفاوت گالوانیزه گرم با گالوانیزه سرد
انجام فرآیند گالوانیزه گرم کمی پیش تر شرح داده شد که به وسیله حوضچه های مذاب فلز روی انجام می گیرد؛ به همین علت نام آن نیز گالوانیزه گرم نامیده شده است. در صورتی که گالوانیزه سرد در دمای محیط و به وسیله اسپری کردن محلول روی، آبکاری الکتریکی یا گالوانیزه الکتریکی انجام می گیرد. در نتیجه می توان گفت اولین تفاوت گالوانیزه گرم و سرد در روش تولید می باشد و سایر تفاوت این دو روش نیز در موارد زیر است:
- سطح ظاهری ورق های گالوانیزه ای که در روش گالوانیزه گرم تولید می شوند، به سبب پوشش روی ضخیم تر، نقره ای رو به خاکستری می باشد؛ در صورتی که ورق گالوانیزه تولید شده در روش سرد، سطح ظاهری بسیار درخشان و نقره ای دارد.
- ضخامت کوتینگ روی در روش گالوانیزه گرم با کنترل کمتری همراه است؛ زیرا این پوشش به وسیله حوضچه ها بر سطح شیت ها اعمال شده و در صورت تنظیم آن باید از روش گاما و … استفاده شود. ضخامت پوشش روی در گالوانیزه سرد کاملاً قابل تنظیم بوده و کمتر از گالوانیزه گرم می باشد.
- میزان مقاومت و استحکام ورق گالوانیزه گرم به علت داشتن پوشش ضخیم تر نسبت به گالوانیزه سرد، در برابر عوامل اکسیدی و رطوبتی بیشتر است.
- طول عمر شیت هایی که در روش گالوانیزه گرم تولید می شوند، به سبب مقاومت و استحکام بالاتر در برابر شرایط آب و هوایی مختلف، بیشتر از شیت های سرد می باشد.
- میزان چسبندگی پوشش در گالوانیزه سرد بسیار کم می باشد و این پوشش به راحتی با یک خراش از بین می رود و سبب زنگ زدگی فلز پایه خواهد شد؛ این در صورتی است که چسبندگی پوشش روی در روش گرم بسیار بهتر بوده و به همین سبب نیز ورق های گالوانیزه گرم مقاومت و طول عمر بیشتری را به خود اختصاص می دهند.
- در نهایت نیز باید گفت تفاوت در این موارد سبب ایجاد تمایز میان کاربرد محصولات حاصل از این دو روش گردیده است. طبیعتاً زمانی که استفاده از فولاد گالوانیزه با مقاومت بیشتر و طول عمر بالاتر مد نظر باشد، از گالوانیزه گرم و اگر تنها سطح ظاهری محصول در نظر گرفته شود، از گالوانیزه سرد استفاده می کنند.
مشخصات گالوانیزه گرم
همان گونه که بیان کردیم، فرآیند گالوانیزه گرم طی غوطه ور کردن ورق های فولادی در حوضچه های مذاب روی صورت می گیرد. دمای این حوضچه ها در حدود 842 درجه فارنهایت یا 450 درجه سانتی گراد می باشد که در طی آن یک پوشش پیوند متالورژی بر سطح ورق ها ایجاد می شود. این پوشش از فولاد زیرین در برابر محیط های سخت و عوامل خارجی و داخلی محافظت می کند. ورق هایی که در این روش تولید می شوند، ضخامتی بین 18/0 تا 4 میلی متر داشته و قابلیت های زیر را نیز به خود اختصاص می دهند:
- مقاومت در برابر عوامل ذکر شده
- انعطاف پذیری و فرم دهی
- قابلیت رنگ آمیزی
- نصب آسان
- وزن سبک
- سازگاری با انواع محیط ها
- قابلیت انجام جوشکاری بر روی آن
- طول عمر و استحکام زیاد
عرض این فلزات نیز بین 1000 تا 1250 میلی متر بوده و اگر به صورت رول عرضه شوند، محدودیتی در طول ندارند. لازم به ذکر است ورق های گالوانیزه گرم در پایان فرآیند تولید، به سبب سرد شدن پوشش، غلظت و ضخامت روی، یک سری عیوبی بر سطح آن ها ایجاد می شود که با نام اسپانگل یا گل گالوانیزه شناخته می شوند. از این رو ورق های گالوانیزه به سه صورت بدون گل، گل ریز و گل درشت در بازار تولید و عرضه می شوند.
مزایای گالوانیزه گرم
استفاده از فرآیند گالوانیزه گرم مزیت های بسیاری دارد که اولین مزیت آن مربوط به ایجاد یک فرآیند دوستانه بین فولاد و محیط زیست خواهد شد. در واقع این فرآیند کمترین آسیب های زیست محیطی را به همراه دارد. از سوی دیگر لایه های آلیاژ روی و آهن متالورژی از نظر کاتدی از فولاد زیرین محافظت می کنند و به عنوان یک مانع میان فولاد و محیط عمل خواهند کرد.
روکش اعمال شده از فلز روی بر سطح این فلزات استحکام بالایی دارد و از این رو محصول نهایی در برابر سایش و ضربه نیز مقاوم است. در واقع با آسیب دیدن لایه های بین فلزی، اتفاقی برای فولاد نمی افتد؛ زیرا پوشش روی از سطح و زیر آن تا حدود 4/1 اینچ محافظت خواهد کرد.
اعمال شدن پوشش گالوانیزه به صورت عمودی سطح فلزات نیز سبب مقاومت و طول عمر بیشتر آن شده و همچنین می توان اطمینان حاصل کرد که پس از اعمال شدن پوشش، تمامی لبه ها و قسمت های مختلف فولاد به صورت یکسان از محافظ سطحی بهره مند شده اند. همین موضوع نیز سبب جبران شدن فضاهای توخالی فولاد زیرین خواهد شد.
تاریخچه گالوانیزه گرم
به طور کلی گالوانیزه گرم دارای سوابق طولانی و کاملاً اثبات شده می باشد که در ابتدا به سال 1742 باز می گردد که پائول ژاک مالوئین در فرانسه یک روش را با پوشش دهی آهن در روی مذاب ابداع کرد. سپس در سال 1772 لوئیجی گالوانی در ایتالیا اصطلاح گالوانیزه را استفاده کرد و فرآیند الکتروشیمیایی میان فلزات را با آزمایش پاهای قورباغه انجام داد. سپس در سال 1801 آلساندو ولتا یک الکترو پتانسیل میان دو فلز را کشف کرد و در نهایت سال 1836 یک شیمیدان فرانسوی به نام استانیسلاساس سورل حق ثبت اختراع را برای پوشش دهی آهن با فلز روی دریافت کرد.
بهتر است بدانید امروزه بیشتر از 600000 تن روی به شکل سالیانه در آمریکا شمالی در تولید فولاد گالوانیزه گرم، 200000 تن برای فرآیند پس از تولید و 400000 تن برای فرآیند گالوانیزه به کار برده می شود.
مراحل گالوانیزه گرم
مراحل انجام فرآیند گالوانیزه گرم شامل سه مرحله اصلی آماده سازی سطح فولاد اولیه، گالوانیزاسیون و بازرسی و تکمیل عملیات است. در ابتدا ضخامت ورق های سرد که با آنالیز شیمیایی مشخص باید گالوانیزه شوند، به وسیله اشعه ایکس کنترل شده و در صورت نیاز قسمت هایی از آن ها بریده می شوند. در بخش بعدی به وسیله محلول های قلیایی که با فشار اسپری می شوند، چربی ها و آلودگی های سطح فلزات را پاکسازی می کنند. این فرآیند به کمک کشیدن برس های نرم و مخصوص فلزات بر سطح و زیر آن ها انجام می شود.
مرحله بعدی شامل شستشوی کامل شیت ها برای از بین رفتن لایه های اسیدی و قلیایی و همچنین باقی مانده چربی ها می باشد که با استفاده از آب تمیز و خالص صورت می گیرد. سپس شیت ها طی فرآیند آنیلینگ گرما دهی شده و بعد به وسیله فن های مخصوص خنک می گردند. در بخش بعدی نیز اتمسفر محافظ بر سطح آن ها اعمال شده تا از اکسید شدن فولاد محافظت شود. در بخش بعدی فرآیند گالوانیزاسیون با غوطه ور شدن شیت ها از حوضچه های مذاب روی انجام گرفته و پس از اعمال پوشش بر زیر و سطح آن ها از حوضچه ها خارج می شوند تا جت هوا بلافاصله به آن ها برخورد کند.
سپس ضخامت کوتینگ روی به وسیله روش گاما مجدداً کنترل و در صورت لزوم به وسیله غلطک های نورد تنظیم می گردد. در پایان پس از سرد شدن کامل شیت های گالوانیزه و بازرسی کیفیت ساختاری، گل گالوانیزه و…، سطح آن ها را برای جلوگیری از شوره زدن کروماته می کنند و بر اساس خواست مشتریان به صورت رول یا شیت بسته بندی می نمایند.