فولاد در چه صنایعی کاربرد دارد؟
فولاد چیست ؟
شاید اگر نام فولاد را بشنوید، یک فلز بسیار محکم در ذهنتان نقش ببندد و بگویید نوعی آهن مستحکم است. اما آیا فولاد یک فلز است؟ درواقع باید گفت خیر! فولاد نوعی فلز نیست بلکه یک آلیاژ است. آلیاژ به ترکیبی از فلزات و نافلزات گفته میشود که در آنها حداقل دو جزء با یکدیگر ترکیبشدهاند. فولاد نیز نوعی آلیاژ است. به عبارتی، در تعریف دقیق، فولاد آلیاژی از آهن و کربن با مقدار کربن بین 0.002 تا 2.1 درصد است و سایر عناصر آلیاژی مانند کروم، نیکل، منگنز و… به مقدار متفاوت در انواع فولادها حضور دارند. آهن، عنصر آلیاژی اصلی در فولادها است و درنتیجه، فولادها یک خانواده بزرگ از آلیاژهای آهنی را تشکیل میدهند.
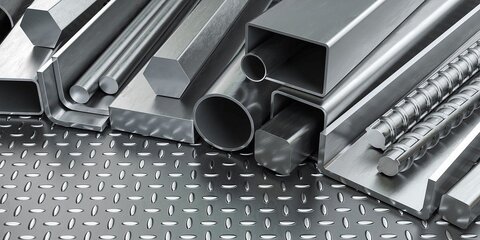
خواص فولاد
فولادها را با استحکام بسیار بالای آنها میشناسیم. اما آیا داشتن تنها استحکام بالا میتواند دلیل خوبی برای تبدیلشدن به یکی از حساسترین مواد صنعتی باشد؟ چه عاملی سبب شده است تا خرید آهن آلات آهن رسان به عضوی جداییناپذیر از صنایع تبدیل شوند؟ بهترین خواص آهن چیست که تا این حد آن را به آلیاژی کارآمد و مهم تبدیل کرده است؟ مهمترین خواص فولادها شامل موارد زیر میشوند:
- استحکام کششی بسیار بالا
- سختی و مقاومت به سایش بالا
- مقاومت به خوردگی بسیار خوب (گریدهای فولاد ضدزنگ)
- دوام و پایداری خیلی خوب در شرایط بارگذاری مختلف
- فراوانی و در دسترس بودن منابع تولید
- شکلپذیری بسیار خوب و قابلیت چکشخواری
- هزینه تولید کم
انواع فولادها کدام اند؟
فولادها براساس فاکتورهای مختلفی طبقهبندی میشوند. برخی از مهمترین این فاکتروها شامل طبقهبندی براساس ترکیب شیمیایی، روش تولید، نوع ریزساختار و … میشوند. در مقاله ، بیشتر با این دستهبندیها آشنا شوید. در اینجا اما فولادها را براساس ترکیب شیمیایی به انواع زیر تقسیمبندی میکنیم:
- فولادهای ساده کربنی
- فولادهای آلیاژی
- فولادهای ضدزنگ
- فولادهای ابزار
فولاد کربنی چیست؟
فولادهای ساده کربنی حاوی مقادیر کمی از عناصر آلیاژی مانند منگنز، سیلیکون و مس هستند. آنها اغلب ازنظر ظاهری مات هستند و 90 درصد از کل فولاد را تشکیل میدهند. فولادهای ساده کربنی براساس میزان کربن موجود در ترکیب شیمیایی آنها، به انواع زیر تقسیم میشوند:
- فولاد کمکربن: حاوی کمتر از 0.3 درصد کربن است و رایجترین فولاد کربنی است.
- فولاد کربن متوسط: حاوی 0.3 تا 0.6 کربن است.
- فولاد پرکربن: این نوع فولاد بالای 0.6 درصد کربن دارد و محکمترین فولاد کربنی است.
فولاد آلیاژی چیست؟
فولادهای آلیاژی حاوی مقادیر مختلفی از عناصر آلیاژی مانند آلومینیوم، کروم، مس، منگنز، نیکل، سیلیکون و تیتانیوم هستند. این عناصر آلیاژی خواص فولاد ازجمله استحکام، شکلپذیری و مقاومت در برابر خوردگی را بهبود میدهند. این فولادها معمولاً ارزانتر هستند و اغلب در قطعات خودرو، ژنراتورهای برق و خطوط لوله استفاده میشوند. فولاد ضد زنگ فولادهای ضد زنگ دارای محتوای کربن کم هستند و معمولاً بین 10.5 تا 30 درصد کروم دارند. استحکام بالا، مقاومت در برابر خوردگی و حفظ استحکام در دماهای بالا ازجمله ویژگیهای فولادهای ضدزنگ است. انواع فولادهای ضدزنگ عبارتاند از:
- فولاد ضد زنگ فریتی (سری 400)
- فولاد ضد زنگ آستنیتی (سری 300)
- فولاد ضد زنگ مارتنزیتی (سری 400)
- فولاد ضد زنگ دوفازی (فریتی + آستنیتی)
- فولاد ضد زنگ رسوب سخت (PH)
فولاد ابزار فولادهای ابزار حاوی مقادیر مختلفی از کبالت، مولیبدن، تنگستن و وانادیوم هستند که آنها را بسیار سخت، بادوام و مقاوم در برابر حرارت میکند. این فولادها برای ساخت ابزارهای فلزی ایدئال هستند و به همین دلیل به آنها فولاد ابزار میگویند. استفاده بهعنوان ابزار برش، انواع تیغهها، ساخت چاقو و… از مهمترین کاربردهای فولاد ابزار است. انواع فولاد ابزار عبارتاند از:
- فولاد ابزار سرد شده در آب (W)
- فولاد ابزار سرد شده در روغن (O)
- فولاد ابزار سرد شده در هوا (A)
- فولاد ابزار کربن بالا- کروم بالا (D)
- فولاد ابزار کارگرم (H)
- فولاد ابزار مقاوم به شوک (S)
- فولاد ابزار تندبر (M , T)
- فولاد ابزار قالب (P)
- فولاد ابزار مخصوص (L)
شرح پروسه فولادسازی[]
دو ماده اصلی در کوره، قراضه و میباشند، ابتدا در کوره مقداری آهن قراضه شارژ میکنند و آن را به وسیله ایجاد قوس الکتریکی ذوب مینمایند و سپس آهن اسفنجی در کوره شارژ مینمایند. خواص فیزیکی قراضه در عملیات ذوب کورههای قوس الکتریکی اثر مهمی دارد. عدم انتخاب صحیح ممکن است منجر به شکستن الکترودها یا سرریز شدن فولاد مذاب یا حتی انفجار گردد در عمل سعی میشود از انواع قراضه در کوره استفاده شود تا معایب به حداقل برسد و عملیات کوره بهینه باشد.
گذشته از مواد اولیه آهن دار که بخش اصلی شارژ کورههای قوس الکتریکی را تشکیل میدهند مواد دیگری به عنوان کمک ذوب، سرباره زا، یا موادی جهت آلیاژ کردن یا تصحیح ترکیب نهایی مذاب مورد نیاز میباشند گاهی افزودن کربن نیز جهت تنظیم نهایی ذوب یا برای بالا بردن مقدار کربن ذوب لازم است. کمک ذوبها که مهمترین آنها آهک است جهت تشکیل سربارهها و اثر گذاشتن بر واکنشهای شیمیایی در مراحل مختلف تصفیه متالوژیکی به کوره افزوده میشوند. عناصر آلیاژ کننده که اکثر آنها مواد فلزی هستند جهت رسیدن به ترکیب نهایی دلخواه به افزوده میشوند. موادی که قسمت زیادی از آلیاژی را دارند فروآلیاژ نامیده میشوند. علاوه بر این مواد، مواد دیگری از قبیل فرومنگنزهای کم کربن و پر کربن و فروسیلیکو منگنز و فروسیلیسیم و سایر فرو آلیاژها نیز افزوده میشوند.
برای افزایش کربن نیز میتوان بهطور مستقیم کربن را به صورت پر کربن وارد کوره نمود یا مواد حامل کربن مثل کک را به شارژ افزود که میزان آن بستگی به نوع فولاد درخواستی دارد. مهمترین ماده کمک ذوب آهک بوده که بازی بودن سرباره نیز بستگی به آن دارد، عمل تصفیه در فولادسازی توسط انتقال مواد از داخل مذاب به سرباره فعال بازی صورت میگیرد. برای عمل خوب و سریع، باید بوده که برای این منظور از مواد روانساز همراه با آهک استفاده میشود. آهک شارژ شده به کوره که نقش مهمی در تشکیل سرباره دارد به سرباره خاصیت بازی نیز میدهد، فصل مشترک بین ذرات آهک و سرباره نقش مهمی در عملیات ذوب دارد بنابراین سعی میشود از ذرات ریز آهک دارای خلل و فرج زیاد استفاده شود.
کم آلیاژ یکی دیگر از مواد مصرفی در کوره، عناصر آلیاژکننده هستند. این عناصر که معمولاً در تولید فولادهای کربنی، پرآلیاژ و فولادهای زنگ نزن مصرف میشود شامل سیلیکون، ، نیکل، و مولیبدن هستند. این عناصر را به صورت ترکیبی با سایر عناصر به فولاد مذاب میافزایند که معمولاً ترکیب با آهن انجام میگیرد گاهی نیز از آلیاژهای دوتایی یا سه تایی که مقدار آهن آن کم است مثل فروسیلیکو منگنز استفاده میشود. دستهبندی فلزات برای ساخت فولاد، دو روش عمده وجود دارد. روش اول استفاده از آهن اسفنجی و برای ذوب آهن اسفنجی و سپس آلیاژسازی است. روش دوم استفاده از (آهن تولید شده در فرایند احیای غیرمستقیم) و سوزاندن کربن اضافی آن است. طی این فرایند میزان کربن آهن خام از بازهٔ ۵٫۳ تا ۶ به ۲٫۰ تا ۱٫۵ درصد وزنی کاهش مییابد، سپس عناصر دیگر در آن افزوده میشوند تا ترکیب مورد نظر بهدست آید.
آهن معمولاً به صورت سنگ معدنی مانند و در یافت میشود. فولاد را با سوزاندن آهن خام سفید و همجوش کردن آن با کمی کربن و اندازه کردن عنصرهای دیگر در آن، به دو روش خمیری کردن و ذوب کردن تولید میکنند. امروزه تقریباً تمامی فولاد جهان از طریق ذوب آهن به روشهای مختلف به دست میآید. این روشها میتوانند شامل فولادسازی در کنورتور یا فولادسازی در کورههای باشد. در روشهایی که از کنوروتور استفاده میشود، آهنخام مذابی که از که فرایند کوره بلند به دست آمدهاست درون کنورتور ریخته میشود تا با استفاده از دمش گاز اکسیژن کربن اضافی آن سوزانده شود. بدین ترتیب کربن فولاد به میزان مورد نظر خواهد رسید. سپس با اضافه کردن عناصر آلیاژی به آن استحکام فولاد افزایش خواهد یافت.
نمایی از برای تولید فولاد در روشهایی که از کورههای قوس استفاده میکنند، ابتدا آهن اسفنجی تولید شده در فرایند احیای مستقیم درون کوره قوس الکتریکی ریخته میشود تا ذوب گردد. دمای این کورهها به حدی است که در همان ذوب اولیه فولاد با درصد کربن نسبتاً پایین تولید میشود. سپس فولاد تولید شده درون کورهٔ پاتیلی ریخته میشود تا در آنجا عملیات آلیاژسازی انجام شود. این عملیات شامل تنظیم کردن میزان کربن، اضافه کردن عناصر آلیاژی و یکدستسازی ترکیب فولاد است. پس از بهدست آمدن مورد نظر در فولاد، لازم است که آن را به صورت مورد نیاز ریختهگری کرد. در اکثر موارد فولاد بهدست آمده به صورت تختال، تیرآهن یا ریختگری مداوم میگردد.
برای ساخت برخی قطعات فولادی که شکل پیچیده یا تیراژ کمی دارند لازم است به صورت جداگانه ریختگری انجام شود که در صنعت به آن فولادریزی گفته میشود. فرایند ذوبریزی فولاد همانند میباشد، چون فولاد مذاب هنگام سرد شدن و انجماد دچار انقباض میشود، بایستی قطعات فولادی را از هر سو ۱٫۵٪ تا ۲٪ بزرگتر ساخت تکه شکا پس از انجماد فولاد مذاب، تکهٔ فولادی به اندازهٔ ساخته شده درآید. آهنگری یا فورجینگ فرآیندی است که در آن با استفاده از نیروی تغییرشکل لازم بر روی فولاد انجام میشود. این تغییر شکل روی فولاد میتواند طی یک یا چند مرحله توسط پتککاری یا پرسکاری انجام شود و شکل نهایی ایجاد گردد. برای افزایش قابلیت شکلپذیری معمولاً به فولاد میدهند تا به حالت خمیری درآید، سپس آن را با پتک میکوبند. یا چکشکاری میکنند تا به خواسته شده در آید.
کاربرد انواع مختلف فولاد[]
از فولادی که تا ۰٫۲ درصد کربن دارد، برای ساختن سیم، لوله و ورق فولاد استفاده میشود. فولاد متوسط ۰٫۲ تا ۰٫۶ درصد کربن دارد و آن را برای ساختن ، و قطعات ساختمانی بکار میبرند. فولادی که ۰٫۶ تا ۱٫۵ درصد کربن دارد، سخت است و از آن برای ساختن ابزارآلات، و کارد و چنگال استفاده میشود. خاصیت سختی و مقاومت بالای آن باعث کاربرد در صنایع خودرو سازی برای تولید قطعات اصلی مانند قابهای خودرو و رینگهای چرخ شدهاست. برخی از انواع فولاد در برابر حرارت بالا و مقاومت بالایی دارند بنابراین از آنها در ساخت انواع مخزن و لوله در پالایشگاهها و کارخانهها و ساخت ابزارهای برش و دقیق استفاده میشود. ورق سیاه معمولی ساختمانی ST-37 که بیشترین مصرف را در بین ورقهای دیگر دارد به سه صورت ورق سیاه رول، ورق سیاه فابریک و ورق سیاه شیت شده یا به اصطلاح بازار ورق سیاه رول برشی معروف هست، تولید و عرضه میگردد.