چطور جلوی کف کردن بیش از حد در فرمولاسیون رنگ صنعتی را بگیریم؟
چطور جلوی کف کردن بیش از حد در فرمولاسیون رنگ صنعتی را بگیریم؟
کف کردن بیش از حد در فرمولاسیون رنگ های صنعتی یکی از چالش های رایج و مهمی است که می تواند پیامدهای ناخوشایندی برای کیفیت نهایی محصول و بهره وری فرآیند تولید داشته باشد. این پدیده نه تنها ظاهر رنگ را نامطلوب می کند بلکه می تواند منجر به ایجاد حباب در فیلم رنگ پس از اعمال کاهش چسبندگی افت براقیت و حتی مشکلات در فرآیندهای پمپاژ و بسته بندی شود. کنترل و پیشگیری از کف نیازمند درک عمیقی از عوامل مؤثر بر آن و به کارگیری راهکارهای تخصصی در تمام مراحل از انتخاب مواد اولیه تا بهینه سازی فرآیند تولید است.
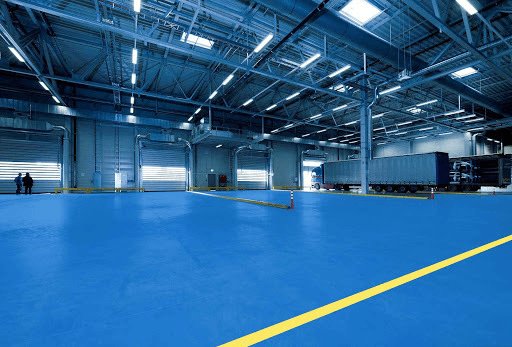
در این مقاله به عنوان یک راهنمای جامع و کاربردی به بررسی دقیق علل اصلی ایجاد کف در رنگ های صنعتی می پردازیم و سپس راهکارهای عملی و اثربخش برای مقابله با این مشکل ارائه خواهیم داد. هدف ما ارائه دانش فنی لازم برای فرمولاتورها و تولیدکنندگان رنگ است تا بتوانند با شناسایی ریشه مشکل بهترین روش ها را برای جلوگیری از کف کردن بیش از حد به کار گیرند و کیفیت محصول خود را ارتقا بخشند.
چرا رنگ صنعتی کف می کند؟ (علل اصلی کف کردن)
کف کردن رنگ های صنعتی پدیده ای پیچیده است که معمولاً ناشی از تعامل چندین عامل به صورت همزمان است. درک صحیح این عوامل برای یافتن راهکار مناسب حیاتی است. شناسایی دقیق علت یا علل اصلی کف کردن در یک فرمولاسیون خاص اولین و مهم ترین گام برای حل پایدار این مشکل محسوب می شود.
مهم ترین دلایل ایجاد کف در رنگ های صنعتی عبارتند از:
- حضور سورفکتانت ها و عوامل فعال سطحی
- ورود و به دام افتادن هوا در حین فرآیند تولید و اعمال
- وجود ذرات جامد ناهمگن یا آلودگی ها
- نوع و خواص شیمیایی رزین و سایر اجزای فرمولاسیون
- شرایط فیزیکی فرآیند مانند دما فشار و سرعت هم زدن
نقش سورفکتانت ها در کف کردن رنگ
سورفکتانت ها (مواد فعال سطحی) اجزای ضروری در بسیاری از فرمولاسیون های رنگ به ویژه رنگ های پایه آب هستند. این مواد برای اهدافی مانند تر کنندگی پیگمنت ها و فیلرها امولسیون کردن رزین ها و ایجاد پایداری در سوسپانسیون ها استفاده می شوند. با این حال ماهیت شیمیایی سورفکتانت ها که تمایل به تجمع در فصل مشترک مایع-هوا دارند عامل اصلی ایجاد و پایداری کف است.
هر سورفکتانت دارای یک تعادل هیدروفیل-لیپوفیل (HLB) مشخص است. انتخاب سورفکتانت با HLB نامناسب برای سیستم رزین و حلال می تواند منجر به تجمع بیش از حد در سطح و افزایش پایداری حباب ها شود. همچنین استفاده از مقدار بیش از حد سورفکتانت حتی اگر نوع آن مناسب باشد به طور مستقیم با افزایش تمایل به کف کردن و پایداری آن مرتبط است.
انواع مختلفی از سورفکتانت ها شامل آنیونی کاتیونی غیر یونی و آمفوتری وجود دارند که هر کدام رفتار متفاوتی در ایجاد و شکستن کف از خود نشان می دهند. سورفکتانت های غیر یونی معمولاً تمایل کمتری به ایجاد کف پایدار نسبت به انواع یونی دارند اما این بستگی به ساختار مولکولی و غلظت آن ها دارد.
تاثیر آلودگی ها و ذرات معلق
حضور ذرات جامد معلق چه به صورت عمدی (مانند پیگمنت ها و فیلرها) و چه به صورت ناخواسته (آلودگی ها) می تواند به شدت بر پدیده کف کردن تاثیر بگذارد. این ذرات می توانند به عنوان هسته هایی برای تشکیل حباب های هوا عمل کنند. همچنین ذرات با سطح آبگریز یا آبدوست خاص می توانند در دیواره حباب ها تجمع یافته و به پایداری آن ها کمک کنند.
آلودگی هایی مانند روغن ها گریس ها باقی مانده های مواد قبلی در تجهیزات یا حتی گرد و غبار محیطی می توانند کشش سطحی رنگ را تغییر داده و منجر به افزایش تمایل به کف کردن یا پایداری کف شوند. اطمینان از تمیزی تجهیزات تولید فیلتراسیون مناسب مواد اولیه و کنترل محیط تولید از نظر آلودگی ذرات معلق گام های مهمی در پیشگیری از این مشکل هستند.
حتی توزیع اندازه ذرات پیگمنت ها و فیلرها نیز می تواند بر کف کردن تاثیر بگذارد. ذرات بسیار ریز یا با توزیع اندازه نامناسب ممکن است در پایداری کف نقش داشته باشند اگرچه نقش اصلی ذرات در کف کردن بیشتر به ماهیت سطحی و نحوه تعامل آن ها با سورفکتانت ها و رزین برمی گردد.
تاثیر سرعت و روش هم زدن
یکی از رایج ترین علل فیزیکی ورود هوا و ایجاد کف در رنگ فرآیند هم زدن و دیسپرس کردن است. هم زدن با سرعت بیش از حد به خصوص در مراحل اولیه که ویسکوزیته پایین است می تواند باعث ورتکس (گرداب) شدید و کشیده شدن حجم زیادی از هوا به داخل مایع شود.
نوع همزن و طراحی پره آن نیز اهمیت دارد. همزن هایی که برای دیسپرس کردن ذرات طراحی شده اند (مانند دیسولورها) در سرعت های بالا مقادیر زیادی هوا را وارد سیستم می کنند. استفاده از همزن های مناسب برای هر مرحله از فرآیند (مانند همزن های پارویی یا لنگری برای مخلوط کردن آرام) و کنترل سرعت همزن بر اساس ویسکوزیته و ماهیت فرمولاسیون برای کاهش ورود هوا حیاتی است.
علاوه بر سرعت نحوه قرارگیری همزن در مخزن شکل مخزن و حجم ماده داخل مخزن نیز بر میزان ورود هوا تاثیر می گذارند. هم زدن نزدیک به سطح مایع یا در مخزن های نیمه پر با همزن های با سرعت بالا احتمال کف کردن را افزایش می دهد. بهینه سازی پارامترهای فرآیند هم زدن بر اساس حجم بچ تولیدی و خواص رئولوژیکی رنگ در مراحل مختلف ضروری است.
راهکارهای عملی برای جلوگیری از کف کردن
پیشگیری و کنترل کف در فرمولاسیون رنگ های صنعتی نیازمند اتخاذ رویکردهای چندوجهی است که شامل انتخاب مواد اولیه مناسب اصلاح فرمولاسیون استفاده از افزودنی های تخصصی و بهینه سازی فرآیند تولید می شود. اجرای موفقیت آمیز این راهکارها به طور معمول نیازمند آزمایش و ارزیابی دقیق در مقیاس آزمایشگاهی و نیمه صنعتی است.
راهکارهای اصلی برای جلوگیری از کف کردن عبارتند از:
- استفاده هوشمندانه از مواد ضد کف (Antifoam Agents)
- اصلاح و بهینه سازی ترکیب شیمیایی فرمولاسیون
- کنترل دقیق کیفیت و خلوص مواد اولیه ورودی
- تنظیم و بهینه سازی پارامترهای فرآیند تولید
ترکیبی از این روش ها معمولاً بهترین نتیجه را در کنترل پایدار کف ارائه می دهد زیرا کف کردن اغلب ناشی از تعامل چندین عامل است.
استفاده از مواد ضد کف (Antifoam Agents)
مواد ضد کف که گاهی به آن ها Defoamer نیز گفته می شود افزودنی های شیمیایی هستند که به طور خاص برای کنترل و از بین بردن کف در سیستم های مایع طراحی شده اند. این مواد با مکانیسم های مختلفی عمل می کنند که رایج ترین آن ها شامل کاهش کشش سطحی موضعی گسترش سریع بر روی سطح حباب ها و ایجاد ناپایداری در دیواره حباب است که منجر به ترکیدن آن ها می شود.
مواد ضد کف معمولاً از ترکیب یک حامل (مانند روغن معدنی یا سیلیکون) و ذرات آبگریز (مانند سیلیس آبگریز شده) تشکیل شده اند. این ذرات آبگریز در فصل مشترک حباب ها جمع شده و باعث شکستن آن ها می شوند. انواع اصلی مواد ضد کف شامل ضد کف های پایه سیلیکون ضد کف های پایه روغن معدنی ضد کف های پلیمری و ضد کف های پایه آب هستند.
انتخاب ماده ضد کف مناسب به شدت به نوع فرمولاسیون رنگ (پایه آب یا پایه حلال) نوع رزین pH دما ویسکوزیته و سایر افزودنی های مورد استفاده بستگی دارد. استفاده از مقدار نامناسب (کم یا زیاد) یا نوع ناسازگار می تواند نه تنها مشکل کف را حل نکند بلکه منجر به مشکلات جدیدی مانند ایجاد عیوب سطحی (مانند چشم ماهی یا کراتر) در فیلم رنگ شود.
اصلاح فرمولاسیون رنگ
یکی از رویکردهای موثر برای کاهش تمایل به کف کردن اصلاح فرمولاسیون اصلی رنگ است. این کار شامل بررسی و تغییر در نوع و مقدار اجزای مختلف فرمولاسیون می شود. به عنوان مثال انتخاب رزینی با خواص کمتر کف زا کاهش مقدار یا تغییر نوع سورفکتانت های مورد استفاده (با حفظ خواص تر کنندگی و پایداری لازم) یا استفاده از حلال هایی که تمایل کمتری به ایجاد کف دارند می تواند مفید باشد.
توزیع اندازه ذرات پیگمنت ها و فیلرها و نحوه دیسپرس شدن آن ها نیز بر کف کردن تاثیر می گذارد. دیسپرس کردن کامل و همگن ذرات می تواند نیاز به سورفکتانت های دیسپرس کننده قوی را کاهش داده و در نتیجه تمایل به کف را کم کند. همچنین کنترل ویسکوزیته فرمولاسیون در مراحل مختلف تولید می تواند بر میزان هوای ورودی در حین هم زدن تاثیر بگذارد.
گاهی اوقات افزودن مقادیر کمی از مواد افزودنی خاص (غیر از ضد کف های اصلی) که به اصلاح کشش سطحی یا پایداری سیستم کمک می کنند می تواند در کنترل کف موثر باشد. این رویکرد نیازمند درک عمیقی از شیمی سطح و تعاملات بین اجزای مختلف در فرمولاسیون رنگ است.
کنترل کیفیت مواد اولیه
کیفیت و خلوص مواد اولیه نقش حیاتی در پیشگیری از مشکلات فرمولاسیون از جمله کف کردن دارد. مواد اولیه ناخالص یا حاوی آلودگی های ناخواسته می توانند به طور مستقیم یا غیرمستقیم باعث ایجاد کف شوند. به عنوان مثال سورفکتانت های با کیفیت پایین یا حاوی ناخالصی رزین های باقیمانده مونومرهای کف زا یا حلال های آلوده به روغن ها می توانند مشکل ساز باشند.
انجام آزمایش های کنترل کیفیت دقیق بر روی هر بچ از مواد اولیه ورودی شامل بررسی خواصی مانند ویسکوزیته pH محتوای جامد و انجام تست های ساده کف کردن روی نمونه های رقیق شده از مواد اولیه می تواند به شناسایی مواد اولیه مشکل ساز قبل از ورود به فرآیند تولید اصلی کمک کند. اطمینان از تطابق مواد اولیه با مشخصات فنی مورد انتظار یک گام پیشگیرانه اساسی است.
همچنین شرایط نگهداری مواد اولیه نیز اهمیت دارد. نگهداری نامناسب می تواند منجر به تغییر خواص شیمیایی یا فیزیکی مواد اولیه شده و پتانسیل آن ها برای ایجاد کف را افزایش دهد. رعایت دستورالعمل های سازنده برای نگهداری مواد اولیه از جمله دما و رطوبت مناسب ضروری است.
بهینه سازی فرایند تولید
حتی با داشتن فرمولاسیون و مواد اولیه مناسب فرآیند تولید نامناسب می تواند منجر به کف کردن بیش از حد شود. بهینه سازی پارامترهای فرآیند تولید به ویژه در مراحل هم زدن دیسپرس کردن و پمپاژ برای به حداقل رساندن ورود و به دام افتادن هوا ضروری است.
- سرعت هم زدن: تنظیم سرعت همزن بر اساس ویسکوزیته و حجم بچ. در مراحل اولیه با ویسکوزیته پایین سرعت باید کمتر باشد. در مراحل دیسپرس کردن سرعت بالا لازم است اما باید بهینه شود تا ورود هوا به حداقل برسد. در مراحل نهایی مخلوط کردن سرعت آرام تر برای خروج هوای به دام افتاده مناسب است.
- نوع تجهیزات: استفاده از همزن ها و پمپ های مناسب برای نوع رنگ و ویسکوزیته آن. پمپ های جابجایی مثبت معمولاً هوای کمتری نسبت به پمپ های سانتریفیوژ وارد می کنند.
- ترتیب افزودن مواد: ترتیب افزودن اجزا می تواند بر نحوه دیسپرس شدن و امولسیون شدن و در نتیجه بر تمایل به کف تاثیر بگذارد. افزودن ضد کف در مرحله مناسب (معمولاً در مراحل اولیه یا میانی) برای اثربخشی حداکثری مهم است.
- دما و فشار: کنترل دما در فرآیند تولید می تواند بر ویسکوزیته و کشش سطحی تاثیر بگذارد. تغییرات فشار در سیستم های پمپاژ نیز می تواند منجر به تشکیل حباب شود.
انجام آزمایش های فرآیندی در مقیاس کوچک و بررسی تاثیر تغییر پارامترهای مختلف بر میزان کف می تواند به شناسایی شرایط بهینه تولید کمک کند.
نکات مهم در انتخاب مواد ضد کف
انتخاب ماده ضد کف مناسب یک گام تخصصی و حیاتی در کنترل کف است. یک ماده ضد کف ایده آل باید بتواند کف را به سرعت و به طور موثر از بین ببرد پایداری خود را در طول زمان حفظ کند و در عین حال هیچگونه تاثیر منفی بر خواص دیگر رنگ مانند چسبندگی براقیت رنگ ویسکوزیته و مقاومت فیلم رنگ نداشته باشد. سازگاری ماده ضد کف با فرمولاسیون رنگ به ویژه با رزین و سایر افزودنی ها از اهمیت بالایی برخوردار است.
- سازگاری (Compatibility): ماده ضد کف باید به خوبی در فرمولاسیون پخش شود اما نه به قدری که کاملاً حل شود. عدم سازگاری می تواند منجر به جدا شدن فاز ایجاد عیوب سطحی (مانند چشم ماهی) یا کاهش کارایی ضد کف شود.
- کارایی (Efficiency): توانایی ماده ضد کف در از بین بردن کف موجود و جلوگیری از تشکیل کف جدید در طول فرآیند و انبارداری. این کارایی باید در غلظت های مصرفی پایین نیز حفظ شود.
- پایداری (Stability): ماده ضد کف باید در شرایط مختلف فرآیند (دما pH تنش برشی) و در طول زمان انبارداری رنگ خواص خود را حفظ کند.
- تاثیر بر خواص فیلم رنگ: اطمینان از اینکه ماده ضد کف باعث ایجاد عیوب سطحی کاهش براقیت تغییر رنگ یا کاهش خواص مکانیکی فیلم رنگ خشک شده نمی شود.
- هزینه: انتخاب ماده ضد کفی که علاوه بر کارایی از نظر اقتصادی نیز به صرفه باشد.
- محیط زیست و سلامت: توجه به مقررات مربوط به ترکیبات آلی فرار (VOC) و سایر ملاحظات زیست محیطی و بهداشتی در انتخاب ماده ضد کف.
بهترین روش برای انتخاب ماده ضد کف انجام آزمایش های مقایسه ای بر روی نمونه های مختلف در شرایط شبیه سازی شده فرآیند تولید و ارزیابی تاثیر آن ها بر روی خواص رنگ نهایی است.
تاثیر دما و رطوبت بر کف کردن رنگ
دما و رطوبت محیط تولید و انبارداری می توانند به طور قابل توجهی بر خواص فیزیکی و شیمیایی رنگ و در نتیجه بر تمایل آن به کف کردن تاثیر بگذارند. افزایش دما معمولاً باعث کاهش ویسکوزیته رنگ می شود. ویسکوزیته کمتر می تواند در حین هم زدن ورود هوا را تسهیل کند و در عین حال خروج حباب های هوای به دام افتاده را نیز آسان تر سازد. تاثیر کلی دما بر کف کردن به تعامل این دو پدیده بستگی دارد.
از طرف دیگر دما بر کشش سطحی نیز تاثیر می گذارد؛ معمولاً با افزایش دما کشش سطحی کاهش می یابد که این خود می تواند پایداری حباب ها را تحت تاثیر قرار دهد. فعالیت و کارایی مواد ضد کف نیز به دما وابسته است. برخی ضد کف ها در دماهای بالاتر عملکرد بهتری دارند در حالی که برخی دیگر ممکن است کارایی خود را از دست بدهند.
رطوبت به ویژه در سیستم های پایه آب می تواند بر سرعت تبخیر آب از سطح رنگ تاثیر بگذارد. تبخیر سریع تر می تواند منجر به افزایش موضعی غلظت سورفکتانت ها در سطح و پایداری بیشتر کف شود. کنترل دما و رطوبت در محیط تولید و نگهداری رنگ به ویژه در مراحل حساس مانند بسته بندی می تواند به کاهش مشکلات ناشی از کف کردن کمک کند.
روش های تست و ارزیابی میزان کف کردن رنگ
برای ارزیابی کمی و کیفی میزان کف کردن رنگ روش های استاندارد مختلفی وجود دارد که به فرمولاتورها و تولیدکنندگان اجازه می دهد تا عملکرد فرمولاسیون ها و مواد ضد کف مختلف را با یکدیگر مقایسه کنند و تاثیر تغییرات فرآیندی را بسنجند. این تست ها معمولاً شامل ایجاد کف به روشی کنترل شده و سپس اندازه گیری حجم یا پایداری کف ایجاد شده است.
- تست حجم کف (Foam Volume Test): در این روش مقدار مشخصی از رنگ یا محلول حاوی اجزای کف زا در یک استوانه مدرج ریخته شده و سپس به روشی استاندارد (مانند هم زدن با سرعت مشخص عبور هوا یا تکان دادن) کف ایجاد می شود. حجم لایه کف تشکیل شده پس از مدت زمان مشخصی اندازه گیری می شود.
- تست پایداری کف (Foam Stability Test): پس از ایجاد کف زمان لازم برای از بین رفتن حجم مشخصی از کف یا زمان مورد نیاز برای از بین رفتن کامل کف ثبت می شود. این تست نشان دهنده پایداری حباب های کف در طول زمان است.
- تست دینامیکی یا فرآیندی (Dynamic or Process Test): این تست ها سعی در شبیه سازی شرایط واقعی فرآیند تولید یا اعمال رنگ دارند. به عنوان مثال رنگ از طریق یک پمپ یا سیستم همزن با سرعت مشخص عبور داده شده و میزان کف ایجاد شده در حین یا پس از عبور از سیستم ارزیابی می شود.
- تست ظاهری روی فیلم رنگ (Appearance Test on Film): پس از اعمال رنگ بر روی یک سطح فیلم رنگ خشک شده از نظر وجود حباب کراتر یا سایر عیوب ناشی از کف ارزیابی می شود. این تست نهایی ترین معیار ارزیابی اثربخشی راهکارهای کنترل کف است.
ترکیبی از این تست ها به ویژه تست های حجم و پایداری کف به همراه تست ظاهری روی فیلم دید جامعی از عملکرد فرمولاسیون در برابر کف ارائه می دهد.
خلاصه از محتوا :
کف کردن بیش از حد در فرمولاسیون رنگهای صنعتی یکی از چالشهای مهم در این حوزه است که میتواند کیفیت نهایی محصول و کارایی فرآیند تولید را تحت تأثیر قرار دهد. این پدیده معمولاً ناشی از عوامل مختلفی مانند حضور سورفکتانتها ورود هوا در حین تولید وجود ذرات جامد و شرایط فیزیکی فرآیند است. سورفکتانتها که به عنوان مواد فعال سطحی در ترکیب رنگها استفاده میشوند نقش کلیدی در ایجاد کف دارند و انتخاب نوع و مقدار مناسب آنها اهمیت زیادی دارد. همچنین کیفیت مواد اولیه در صنعت بسیار تعیینکننده است؛ ناخالصیها یا آلودگیهای موجود در مواد اولیه میتوانند تمایل به کف کردن را افزایش دهند و مشکلاتی مانند کاهش چسبندگی افت براقیت و ایجاد عیوب سطحی در رنگ نهایی ایجاد کنند.
برای کنترل کف راهکارهایی مانند استفاده از مواد ضد کف (آنتیفومها) اصلاح فرمولاسیون کنترل کیفیت مواد اولیه و بهینهسازی فرآیند تولید به کار گرفته میشود. مواد ضد کف با کاهش کشش سطحی و ناپایدار کردن حبابها از ایجاد و پایداری کف جلوگیری میکنند. انتخاب ضد کف مناسب باید با توجه به نوع فرمولاسیون شرایط فرآیند و سازگاری با سایر اجزا انجام شود.
در کنار این اقدامات مدیریت صحیح فرآیندهایی مانند همزدن کنترل دما و فشار و طراحی بهینه تجهیزات نیز نقش مهمی در کاهش کف دارد. استفاده از مواد اولیه باکیفیت و رعایت استانداردهای نگهداری آنها در صنعت از بروز مشکلات ناشی از کف جلوگیری میکند. در نهایت تستهای استاندارد برای ارزیابی میزان کف و عملکرد ضد کفها به تولیدکنندگان کمک میکند تا بهترین ترکیب مواد اولیه در صنعت را برای تولید رنگهای باکیفیت انتخاب نمایند.
سوالات متداول در مورد کف کردن رنگ های صنعتی
چه عواملی باعث ایجاد کف در رنگ های پایه آب می شوند؟
رنگ های پایه آب به دلیل وجود آب و استفاده گسترده از سورفکتانت ها برای امولسیون و دیسپرسیون تمایل بیشتری به کف کردن دارند. سورفکتانت ها هم زدن شدید آلودگی ها و برخی رزین های خاص از عوامل اصلی کف در این نوع رنگ ها هستند.
بهترین نوع ماده ضد کف برای رنگ های اکریلیک کدام است؟
برای رنگ های اکریلیک پایه آب معمولاً از ضد کف های پایه سیلیکون امولسیون شده یا ضد کف های پلیمری استفاده می شود. انتخاب دقیق بستگی به ویسکوزیته محتوای جامد و سایر افزودنی های فرمولاسیون اکریلیک دارد و باید با تست مشخص شود.
چگونه می توانم بفهمم که ماده ضد کف من به درستی کار می کند؟
با انجام تست های حجم و پایداری کف بر روی نمونه رنگ حاوی ماده ضد کف و مقایسه آن با نمونه بدون ضد کف یا با ضد کف های دیگر. همچنین بررسی فیلم رنگ خشک شده از نظر عدم وجود حباب و عیوب سطحی نشان دهنده عملکرد صحیح ضد کف است.
آیا کف کردن رنگ می تواند بر خواص چسبندگی آن تاثیر بگذارد؟
بله حباب های هوای به دام افتاده در فیلم رنگ می توانند نقاط ضعف ایجاد کرده و سطح تماس رنگ با زیرآیند را کاهش دهند که این امر می تواند منجر به کاهش چسبندگی پوسته شدن یا سایر مشکلات مربوط به اتصال شود.
چگونه می توانم از ایجاد حباب در رنگ بعد از اعمال آن جلوگیری کنم؟
کنترل کف در فرمولاسیون و فرآیند تولید اولین قدم است. همچنین استفاده از روش های اعمال مناسب (مانند غلتک یا اسپری با فشار و سرعت صحیح) آماده سازی سطح مناسب زیرآیند و اطمینان از عدم وجود آلودگی یا رطوبت در سطح کمک کننده است.
منبع محتوا : شیمی صنعت